Digitala tvillingar ska lösa mysteriet
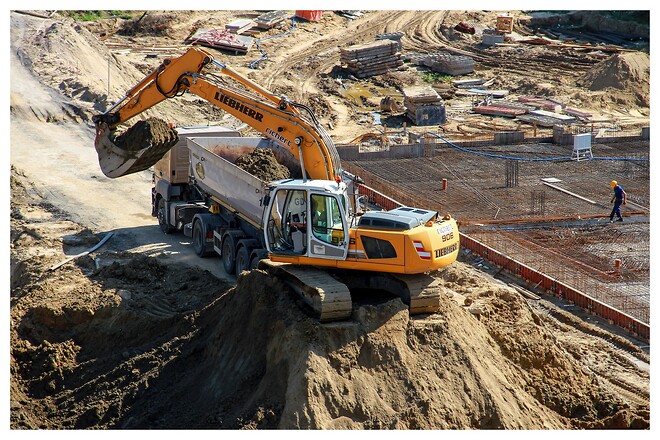
Hur kan digitalisering och AI (artificiell intelligens) öka produktiviteten i anläggningsbranschen? Frågan togs upp på det webbsända seminarium som Infrasweden2030 anordnade i slutet av april.
Temat för webinariet var ”Erfarenheter av digitalisering och implementering av AI-teknologi” och en av talarna var Peter Eriksson på forskningsinstitutet Blue Institute.
Han representerade Piia (process industrial IT and automation) och talade om forskningsprojektet Construction Factory, som genomförs i samverkan med MDH, Rise, Volvo CE, Sandvik, Skanska och Trafikverket.
I projektet utgår parterna från ett välkänt faktum; att anläggningsbranschen ligger långt efter andra branscher när det gäller förmågan att öka sin produktivitet.
– Bygg- och anläggningsbranschen är en av de största sektorerna i ekonomin och utgör på global basis ungefär 13 procent av BNP, sade Peter Eriksson.
– En utmaning här är att medan tillverkningsindustrin har ökat sin produktivitet med cirka tre procent per år så har anläggningsbranschen under flera decennier nästan stått still.
Målet är att hitta lösningar på detta, med särskilt fokus på väginfrastruktur, bergtäkter och asfaltproduktion.
Peter Eriksson noterade flera anledningar till att produktiviteten inte ökat på samma sätt som i till exempel tillverkningsbranschen: bristen på information gör att sämre beslut fattas, avsaknaden av detaljerad kunskap från tidigare projekt leder till dålig planering, maskinrörelserna koordineras inte optimalt, arbetet kan inte följas i realtid och uppföljningen är inte heller så bra som den borde vara
– Tillsammans gör det att många förbättringar uteblir.
Projektets ansats har varit att titta på hur tillverkningsindustrin och processindustrin gör, och inspireras av det.
Branscherna skiljer sig dock åt på många sätt. Anläggningsprojekten utförs utomhus, i skiftande och delvis okänd terräng. En väg är sällan den andra lik, processen är kort och varierande, dessutom är det många aktörer inblandade.
I projektet har man ändå försökt hitta inspiration från process- och tillverkningsindustrin.
– Andemeningen är att betrakta framtidens byggnation som ett system av system, där alla tillgångar är digitaliserade och integrerade mot att leverera produkter enligt BIM.
Målet är att kunna sätta upp och konfigurera ”anläggningsfabriker” när och var som helst.
– Man kan till exempel identifiera hela vägen från berg till väg eller spår, som en process i flera steg, förklarade Peter Eriksson.
Processen har fått namnet ”rock to road”, eller ”rock to rail” och i flödet ingår allt, både material, maskiner och logistik.
– Vi betraktar produktionsflödet som en virtuell fabrik, det är berg i ena änden av linan, färdig asfalterad väg i den andra.
Tanken här att modularisera processen, sedan ska man kunna skapa nya kombinationer av de moduler som finns, och skräddarsy fabriken för det projekt den ska användas i.
– Allt ska leverera mot den modell av produkt som är sökt i BIM – man kan betrakta hela systemet likt ett krypto, där rätt kombination ger maximal effektivitet.
För att få detta komplicerade nätverk att fungera krävs digitalisering där alla delar kommunicerar.
– Det handlar om att bygga digitala modeller av borriggar, krossverk, hjullastare med mera, med deras egenskaper och beteenden.
När arbetet sedan är i gång ska alla maskiner och andra komponenter rapportera in väsentlig data, information som direkt bygger på den befintliga BIM-modellen.
– Då kan vi bygga lärande till planeringen av kommande projekt.
Processen måste vara flexibel. Slitaget i ett krossverk gör till exempel att kapaciteten varierar och det påverkar den efterföljande logistiken – risken finns att lastmaskinerna står och väntar när krossverket inte levererar i samma takt.
Här kan koncepten Lean och Just-in-time komma till nytta, särskilt om maskinerna kan kommunicera med varandra digitalt, påpekar Peter Eriksson.
– Genom att bygga digitala tvillingar av krossverket och efterföljande maskiner kan den här informationen utbytas mellan maskinerna och takten kan justeras.
Genom att skapa förarstöd eller automatisera processen kan energiåtgången reduceras, miljön påverkas mindre och maskinerna slits dessutom mindre, förklarade Peter Eriksson.
– Då behöver vi en produktionsstyrning som kan hantera den varians som finns i projekten, där de här lösningarna kan integreras och vidare möjliggör ännu större värdeskapande då data delas över hela värdekedjan, från prospektering, projektering till kvalitetskontroll och underhåll av anläggningar.
Han listar flera stora utmaningar i projektet, som än så länge bara finns på simuleringsnivå.
Att beskriva och spåra massor, till exempel grus, är inte helt lätt. Det kräver också stora insatser om man ska kunna designa en arkitektur som gör det möjligt att integrera alla tillgångar i systemet.
– Lösningen i sin helhet är en bit bort. Men det fungerar bra som ett integrerande koncept där företag kan samverka och stegvis realisera del för del.